Case Study
Edge Computing in Specialty Chemicals
How EOSYS modernized a specialty chemicals manufacturer’s batch infrastructure in just 10 weeks with Stratus Edge Computing
Challenges
- Outdated legacy hardware and software
- Frequent unplanned downtime
- Multiple, disconnected physical hosts running different software
- Difficulty facilitating repairs and fixes due to limited staff
Solution
- Stratus ftServer®
- Rockwell Automation
- FactoryTalk View
- FactoryTalk Historian
- FactoryTalk Batch
- FactoryTalk Transaction Manager
- FactoryTalk Directory
- Engineering workstation running SE and ControlLogix PLC
- VMware Veeam
Benefits
- Consolidated 9 server workloads and processes onto a single Stratus ftServer
- Access to 24/7 Stratus Support and Services
- Updated and modernized legacy systems
- Eliminated unplanned downtime
EOSYS is a trusted, employee-owned system integrator, recently named System Integrator of the Year by Control Engineering for delivering innovative technical solutions to automate, monitor, and secure customers’ industrial systems. They have expertise in several industries,
ranging from chemical manufacturing and food & beverage to building products and pulp & paper, with offices covering customer sites across the United States. The company employs dedicated platform and distributed control system subject matter experts for Rockwell, AVEVA,
Wonderware, Ignition, Siemens, GE, and more, which allows EOSYS to be extremely flexible for their customers for critical implementations.
Because of their wealth of experience, they were selected by a leading global specialty chemicals manufacturer to recommend, design, and implement a phased program to modernize compute infrastructure across product lines. The solution was a Stratus Edge Computing platform. The specialty chemicals manufacturer plays an important role in sustainability and green technology by producing catalysts essential for reducing emissions of light and mid-duty internal combustion engine (ICE) vehicles. These vehicles range from automobiles and motorcycles to diesel-powered trucks, tractors, and trains.
The company was experiencing several production disruptions because of disconnected processes, legacy computing infrastructure, frequent unplanned downtime, and difficulty facilitating repairs and fixes due to limited staff – challenges common to many manufacturers managing long life assets and established production lines. To address these challenges, it was essential for the chemical manufacturer to streamline and consolidate complex processes, eliminate unplanned downtime, and update and modernize legacy servers to avoid disruptions that were not only costly, but potentially hazardous. With EOSYS and Stratus Edge Computing, the company has successfully addressed these challenges by modernizing their infrastructure and eliminating unplanned downtime.
Legacy systems and aging computing infrastructure hardware disrupt operations with unplanned downtime and lack of data reliability
To update their customers’ environment and simplify operations, EOSYS recommended consolidating hardware and software to simplify both footprint and manageability, while continuing with, and updating Rockwell Automation applications. The chemical manufacturer relied on Rockwell Automation-based systems to run their slurry batching process, which was controlled by nine (9) physical hosts. This process comprised of three (3) FactoryTalk batch servers, two (2) FactoryTalk HMI servers, one (1) Historian server, one (1) SQL server, a domain controller, and an engineering workstation.
The hardware was getting to the end of life, and they were running on the Windows Server 2008 R2 operating system, which lead to problems with the reliability of both the servers and the software. Additionally, the backup domain controller was not synchronized and had not been for
quite some time. Not only that, but the secondary HMI server would occasionally disconnect.
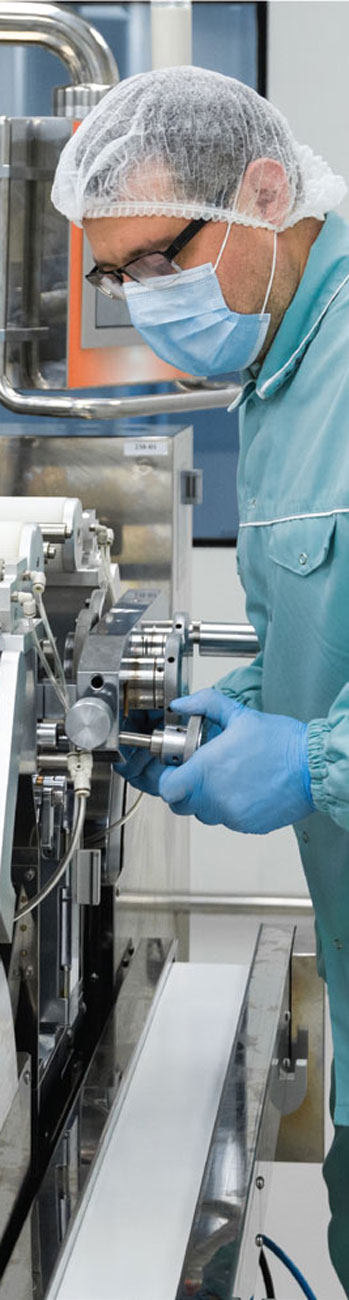
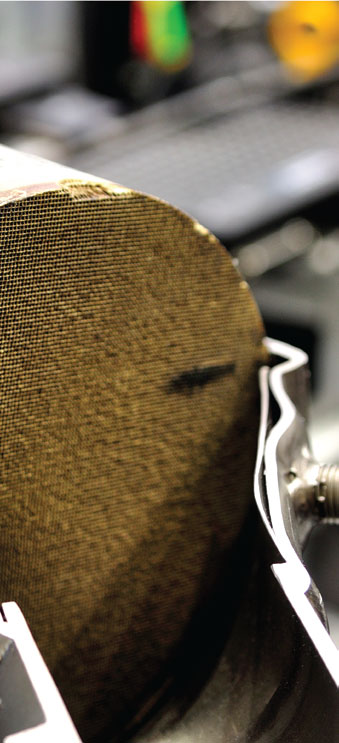
Chase Davis
Director of Technology for Automation
EOSYS
Of significant concern, the company was running in a non-redundant mode without knowing it. Their system would often lock up and OT personnel would have to reboot the machines frequently. Without a dedicated IT staff, the company’s small OT team – comprising one on-site OT engineer and one controls engineer – would receive calls at any time, day, or night, to maintain and fix these systems. They had limited expertise on the products they had, which made it difficult to troubleshoot and repair the problem, and they were not spending time monitoring both the processes and maintenance on the machines.
The final server failure was the last straw, causing a huge amount of unplanned downtime. It took days for the chemicals manufacturer to rebuild the server, which was a major interruption to operations. After that, they knew it was time to upgrade their hardware and turned to EOSYS for support.
The company modernized systems and eliminated downtime by choosing Stratus
After that final server failure, it was clear the company had to modernize their aging hardware, which presented the opportunity to explore consolidating software workloads on to a single production server. EOSYS presented a few options but recommended moving forward with
the Stratus ftServer® with emphasis on the platforms fault tolerance, explaining that if they lost a CPU or motherboard, for example, they would experience no downtime.
After carefully considering the options presented by EOSYS, the chemicals manufacturer chose to move forward and modernize their multiple systems – 9 physical servers with separate jobs, which took up a lot of rack space – and replaced them with a single, fault tolerant Stratus ftServer. Without making this change, they were at risk of exposing themselves to a lot of downtime with their aging servers. Choosing the Stratus ftServer also solved IT support concerns, providing access to 24/7 Stratus Support Services. With a limited OT staff of just
two, the company no longer needs them, on call to fix and repair systems.
It made the most sense financially and logistically to move over to the Stratus platform. Not only was uptime availability essential for them, but being able to easily maintain the system, consolidate critical workloads, and have access to impeccable service support – including Stratus’ next-day SLA on server replacement parts – was of the utmost importance.
It took ten (10) weeks from start to finish for EOSYS to implement and deploy the Stratus ftServer in the company’s data room, which included spinning up new virtual machines (VMs), installing software, and importing and testing applications. Once the platform was racked in and communications were tested and verified, it took just two (2) days to do the cutover.
The company is running several VMs and different software packages on the ftServer, including two (2) domain controllers, two (2) FactoryTalk view SE servers, one (1) FactoryTalk Historian, three (3) FactoryTalk batch servers, an engineering workstation – with SE and ControlLogix’s
PLC development software running, a SQL server running FactoryTalk transaction manager, a FactoryTalk directory server, and a VMware Veeam server. Since the implementation and upgrade, there has been no downtime.
24/7 Stratus Support services enable continuous operations, no downtime, and no data loss
The company has access to Stratus services and support, which was a huge selling point in choosing the ftServer. Stratus provides proactive services that focus on preventing downtime and data loss before it occurs. An Automated Uptime Layer (AUL) is embedded into every
ftServer platform, which monitors over 500 system alarms to identify, handle, and report faults before they impact the system. Without having to place an order, Stratus services will automatically order the correct customer-replaceable part if a component need replacing.
Since using Stratus Edge Computing, the company has seen zero unplanned application downtime and continuous operations. The controls engineer and OT network engineer have also not had to be called in at odd times to fix and repair failures, freeing up their time to work on other important, business-critical tasks. EOSYS helped the chemicals manufacturer consolidate the multiple servers they had running into a single, fault-tolerant ftServer, odernizing their infrastructure and eliminating costly, unplanned downtime. Currently, the company is getting ready to implement its second ftServer after seeing outstanding success partnering with EOSYS to deploy Stratus computing platforms.
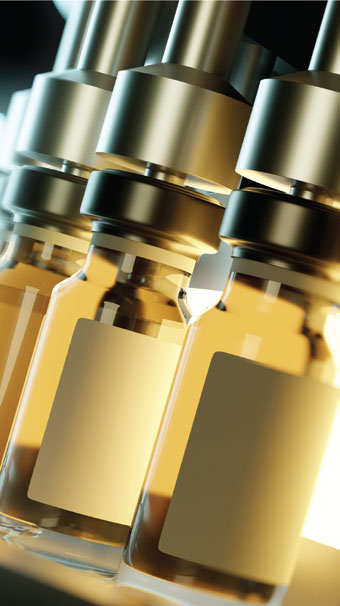
Chase Davis
Director of Technology for Automation
EOSYS