Case Study
SDI Element Logic
Edge Computing in Automated Material Handling
How SDI Element Logic brings its warehouse management solutions to new heights using the power and reliability of Stratus Edge Computing.
Challenges
- Develop material handling and warehouse automation systems with maximum reliability, data accuracy and ability to scale
- Meet customer SLAs for distribution center volume and velocity
- Innovate for company growth and reputation with customers
Solution
- Stratus® ftServer® 6910 platform
- SDI Element Logic warehouse execution system/warehouse control software
- SDI Element Logic unit sortation equipment
- Beckhoff PLC
Benefits
- Consolidated multi-node hardware clusters to a single Stratus platform
- Eliminated downtime, reduced IT costs, and reduced IT support calls by 80%
- Surpassed customer SLAs with greater than 98% accuracy
- Enabled customers to reduce manual labor by up to 50%
- Laid foundation for predictive maintenance, distribution forecasting, and AI
SDI Element Logic has been offering turnkey material handling systems and solutions to brands all over the world since 1977. They are specialists in apparel sortation, unit handling, consulting, engineering and design, systems, and software integration. SDI integrates various innovative technologies such as Joey Pouch Sorter and Enzo AGV, and manufactures their own Tilt Tray Sorter and SORTRAK G4 a Bombay-style unit sorter. Headquartered in Los Angeles, California, SDI services domestic and international clients with operations across the Americas and has more than 400 distribution center systems installed.
Anticipating the need to innovate to meet increasing supply chain and distribution center challenges, the company was well-positioned to address the massive shift in consumer demand and accelerated the need for warehouse automation amid COVID. The company selected Stratus Edge Computing platforms to provide performance and scale, backed by fault tolerance, to power its complex sortation systems without downtime or data loss. With the reliability and simple management of Stratus platforms, SDI Element Logic has successfully delivered a range of cutting-edge solutions to exceed customer SLAs and lay a foundation for more advanced automation, analytics, and AI.
Using Stratus Edge Computing, SDI Element Logic runs its warehouse execution systems (WES) connected to 3PL and ERP systems with zero downtime. Customers have a single pane of glass visibility into their warehouse operations and data availability for predictive maintenance and labor forecasting. With the increased automation and reliability, SDI Element Logic has enabled retailers to reduce manual labor by up to 50% while maintaining 98% accuracy on unit sortation. Stratus also enables SDI Element Logic’s customers to reduce their IT footprint from complex
clusters to a single system, and reduced IT support calls by 80%.
Supply chain and distribution pressures increasing
pre-pandemic
Before the global COVID pandemic, retailers faced several increasing pressures on inventory, warehousing, and distribution. From supporting e-commerce and wholesale operations simultaneously to managing 20-30% increases in product returns, several dynamics placed additional strain on distribution centers that also relied largely on manual processes and labor.
Customers are pushing for less IT infrastructure in the warehouse, often with only a single rack for an entire building. Similarly, organizations require a simpler IT learning curve which also means a drive for fewer vendors for IT to support.
SDI Element Logic recognized their need to transform and modernize existing warehouses to meet the demand for more output and even greater efficiency, as well as to deploy state-of-the-art solutions for greenfield sites. The company’s key differentiator is in unit sortation working with individual parcels inside a box, rather than the boxes to increase automation to reduce labor requirements. It is also an essential solution for retailers and 3PL companies to become more efficient and grow inside their existing four walls. Ultimately, success with customers
means:
- Match or exceed the current rate
- Work in a smaller footprint
- Use less labor to perform the same workloads
- Achieve all those goals while maintaining accuracy and data quality
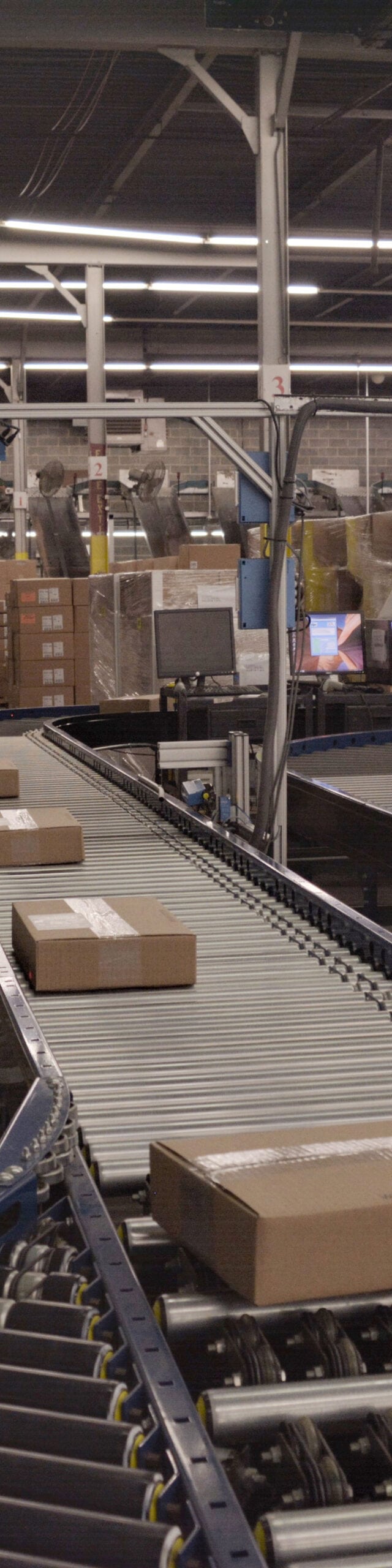
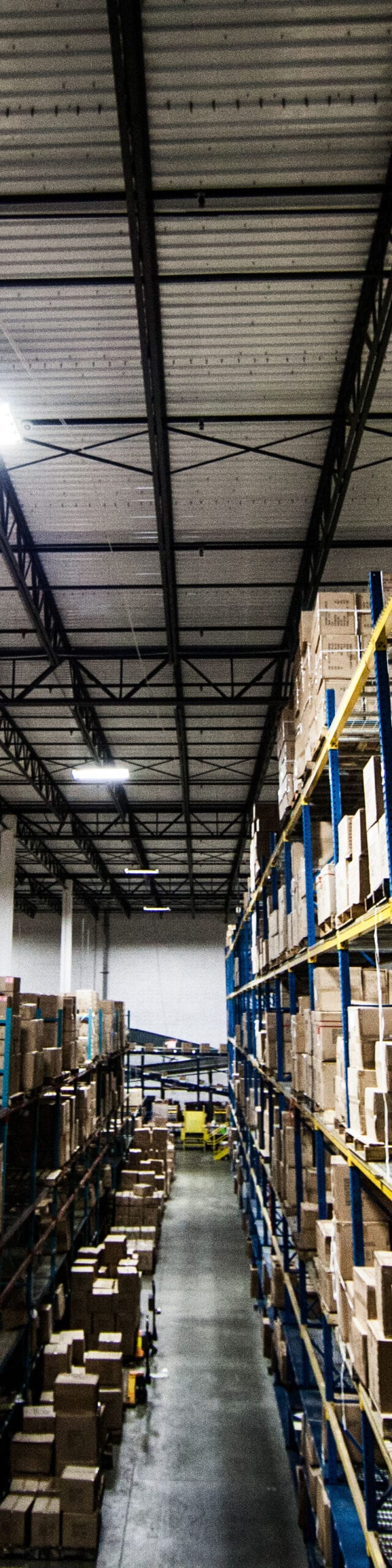
During the pandemic, supply chain and material handling challenges exacerbated the capacity and growth challenges that material handling professionals already faced. According to SDI Element Logic, “COVID pretty much took what probably would’ve happened over five to ten years and pressed it into two.” However, with SDI Element Logic’s focus on innovation, the company was well prepared to meet the unprecedented warehousing challenges of the pandemic.
Edge Computing purpose-built for the rigors and velocity of material handling
Downtime at even a small or mid-size distribution center for a day can equate to $1M in costs. SDI Element Logic, therefore, required computing redundancy to avoid downtime, data loss, and computing power to maintain pace with the high-velocity sortation systems. For many years, the company has turned to Stratus Edge Computing to provide fault tolerance, simplify IT infrastructure, and ensure maximum reliability to match its material handling solutions. The reliability of the platform provides a foundation for customer innovation.
The Stratus ftServer serves as the “heart and brain” for SDI Element Logic’s solutions as a one-stop shop for fault tolerance for all critical warehouse applications. The platform provides virtualization to run multiple applications in a single system, and scale to support I/O required in warehousing solutions.
Stratus’ OPC connectively provides HMI visibility into ftServer’s health right alongside the health of other warehouse systems ensuring consistency in how customers interact with equipment. This connectivity also enables a single pane of glass visibility outside the warehouse and into the cloud.
In SDI Element Logic’s architecture, Stratus ftServer typically runs three layers of software warehouse execution software (WES)/warehouse control system (WCS), warehouse management system (WMS), and data connections to SAP and 3PL systems. The platform also includes a web interface and a host interface for communication with customers. By moving the business logic and network control into the ftServer, SDI Element Logic can buy smaller PLCs, shifting them to become off-the-shelf components and reducing the cost of their warehouse automation system architecture.
Shop floor visibility
Through the Stratus ftServer, SDI Element Logic software facilitates every layer inside warehouses, and the company can harvest data from its proprietary solution to drive analytics. With the increase in volume, customers are asking for more analytical data from their equipment to use with AI to recommend proactive maintenance and to do performance trending to avoid labor shortages with demand spikes.
In previous architectures, the company might buy one server for remote management, one for applications, and one for SQL, which introduced the risk that if one fails, the distribution center stopped. At the request of some customers, SDI Element Logic provided alternative six-tier,
six-node hyperconverged solutions but ran into network bottlenecks and found that these more complex solutions were not cost-effective. Replacing these solutions with a single Stratus Edge Computing platform drastically reduced IT infrastructure, cutting rack space by half and replacing three to four different vendors with a single one, Stratus.
The result was a new level of stability and uptime for customers. SDI Element Logic additionally increased its level of service by leveraging Stratus Support for proactive hardware replacement and health monitoring to detect issues in advance. Stratus’ health monitoring reduced SDI Element Logic’s server-related support calls by 80% and reduced platform downtime to zero.
Customer success with SDI Element Logic and Stratus
Stratus provides the Edge Computing foundation enabling SDI Element Logic to meet expectations for some of the top brands in the world.
One big apparel retail company needed a solution that maintained an 89.5% SLA pick ticket within 24 hours. With SDI Element Logic’s solution powered by Stratus, this SLA never dipped below 90% on startup and achieved greater than 98% with the 1.5% error due to human error, rather than system architecture. The solution allowed Lacoste to reduce labor by 30-40%.
SDI Element Logic built a new system for another large apparel retailer inside a 9,000-square-foot distribution center, providing approximately an extra 20,000 square feet of space by building vertically with a second-level mezzanine. This allowed them to cut their retail packing footprint in half from the previous process (from 200,000 to 100,000), as well as dramatically improve unit per hour (UPH) metrics and reduce labor by 50%. As a result, overall department productivity almost doubled from the low-400s UPH to the mid-700s UPH. Packing function productivity also soared from the mid-500s to the low 1,000s.
Another major retailer required an e-commerce sortation system for 6,000 units an hour in a space 25% the size of a traditional unit sorter. SDI Element Logic introduced its proprietary joey sorter which used vertical space and reduced the need for manual operators by 30-50%
over traditional unit sortation solutions. The Stratus platform supports data from 138 Cognex cameras being triggered three times a second, translating to 4,000 MB/s worth of written data to the database.
More innovation ahead for SDI Element Logic and material handling
SDI Element Logic offers a high-performance solution for retailer’s mission-critical applications, and using Stratus ftServer allows the company to serve a range of material handling scenarios with only minor modifications to the platform’s configurations. The repeatable architecture and customization also make it ideal to enable growth.
Among the business benefits of SDI Element Logic, ftServer enables:
- On-site commissioning time under 2 weeks
- Reduced service interruptions due to platform fault tolerance and redundancy
- Fewer support calls by eliminating platform downtime and simplifying the IT architecture
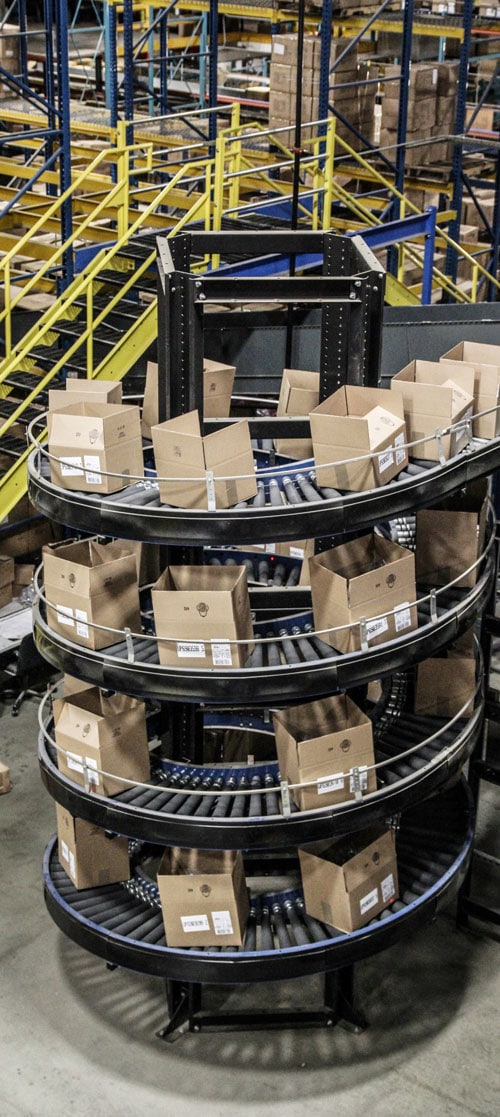
“Stratus ftServer is the heart and brain of our design architectures for running our WMS software and business rules. Downtime at
a distribution center can cost a retailer as much as a million dollars a day, and the Stratus
platform has not let us down. Therefore, we measure Stratus not just by the value of risk
avoidance but by the relationships and credibility that’s enabled our business to
grow consistently and achieve new levels.”
Post-COVID, technology adoption is happening at a much faster pace in material handling with customers looking to adopt analytics-driven systems to make business decisions.
According to SDI Element Logic, “Retail automation companies’ priorities have had to adjust, putting a much bigger influence on automation, logistics, robotics even AI and forecasting, because all those things allow them to mitigate what we just saw with COVID.”
SDI Element Logic continues to turn to Stratus Edge Computing to provide the system reliability to run its novel material handling solutions and platform to innovate for customers.
Stratus ftServer platform running:
- SDI Element Logic warehouse execution system
- SDI Element Logic warehouse control software
- SDI Element Logic unit sortation equipment
- Beckhoff PLC
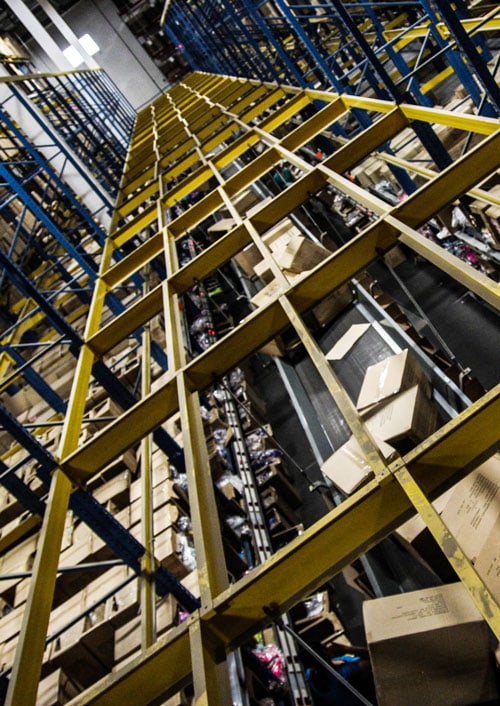