Whitepaper
Deploy Edge Computing to Accelerate Digital Transformation
Transform Operations with Data from the Operational Edge
Modern, distributed computing architecture overcomes operators’ unique IT challenges and brings asset performance, monitoring and control, and logistics visibility outside the fence.
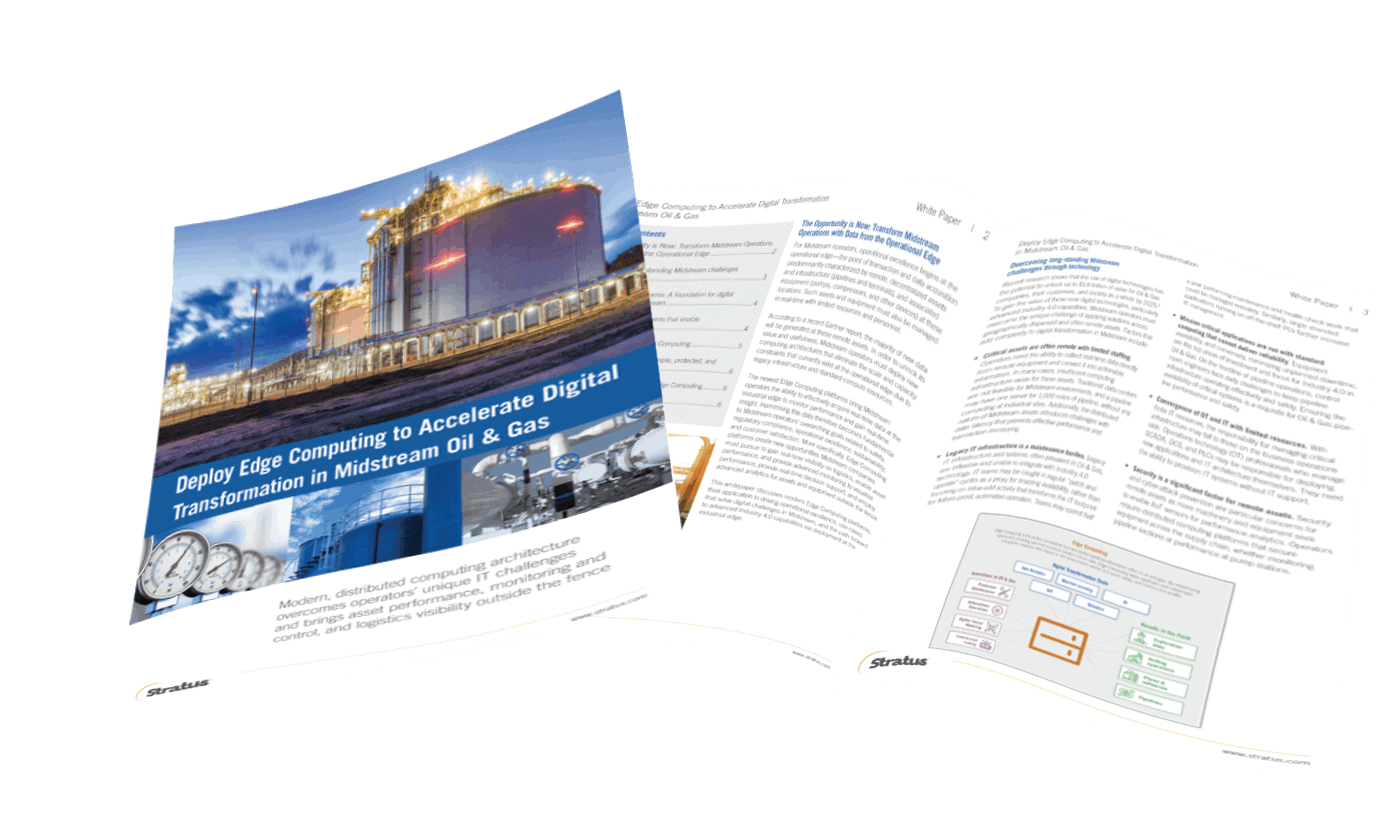
The Oil and Gas whitepaper discusses Edge Computing platforms and their application in driving operational excellence. With Edge Computing operators have the ability to effectively acquire real-time data to monitor performance and gain real-time insight.
Read this whitepaper to learn about:
- Modern Edge Computing platforms
- How Edge Computing enables applications that drive operational excellence
The Opportunity is Now: Transform Midstream Operations with Data from the Operational Edge
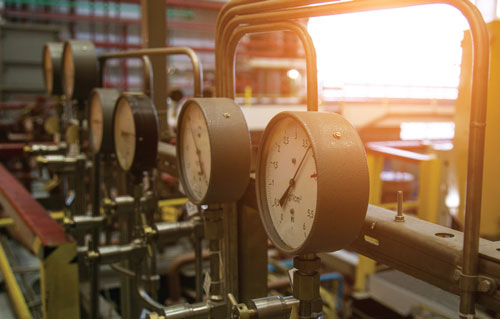
For Midstream operators, operational excellence begins at the operational edge—the point of transaction and data acquisition predominantly characterized by remote, decentralized assets and infrastructure (pipelines and terminals), and associated equipment (pumps, compressors, and other devices) at these locations. Such assets and equipment must also be managed in real-time with limited resources and personnel.
According to a recent Gartner report, the majority of new data will be generated at these remote assets. In order to unlock its value and usefulness, Midstream operators must deploy new computing architectures that eliminate the scale and capacity constraints that currently exist at the operational edge due to legacy infrastructure and standard compute resources.
The newest Edge Computing platforms bring Midstream operators the ability to effectively acquire real-time data at the industrial edge to monitor performance and gain real-time insight. Harnessing this data therefore becomes fundamental to Midstream operators’ overarching goals related to safety, regulatory compliance, operational excellence, sustainability, and customer satisfaction. More specifically, Edge Computing platforms create new opportunities Midstream companies must pursue to gain real-time visibility on logistics, enable asset performance, and provide advanced monitoring to visualize performance, provide real-time decision support, and employ advanced analytics for assets and equipment outside the fence.
This whitepaper discusses modern Edge Computing platforms, their application in driving operational excellence, use cases that solve digital challenges in Midstream, and the path forward to advanced Industry 4.0 capabilities via deployment at the industrial edge.
Overcoming long-standing Midstream challenges through technology
Recent research shows that the use of digital technologies has the potential to unlock up to $1.6 trillion of value for Oil & Gas companies, their customers, and society as a whole by 2025.1 To gain the value of these new digital technologies, particularly advanced Industry 4.0 capabilities, Midstream operators must overcome the unique challenge of applying solutions across geographically dispersed and often remote assets. Factors that add complexity to digital transformation in Midstream include:
- Critical assets are often remote with limited staffing. Operators need the ability to collect real-time data directly from remote equipment and convert it into actionable information. In many cases, insufficient computing infrastructure exists for these assets. Traditional data centers are not feasible for Midstream environments, and a pipeline may have one server for 1,000 miles of pipeline, without any computing at individual sites. Additionally, the distributed nature of Midstream assets introduces challenges with data latency that prevents effective performance and transaction monitoring.
- Legacy IT infrastructure is a maintenance burden. Legacy IT infrastructure and systems, often prevalent in Oil & Gas, are inflexible and unable to integrate with Industry 4.0 technology. IT teams may be caught in regular “patch and update” cycles as a proxy for enabling availability, rather than focusing on value-add activity that transforms the IT footprint for future-proof, automated operation. Teams may spend half a year performing maintenance and health check work that could be managed remotely. Similarly, single stranded applications running on off-the-shelf PCs further increase IT management.
- Mission critical applications are run with standard computing that cannot deliver reliability. Equipment availability, and conversely, minimizing unplanned downtime, are the top areas of investment and focus for Industry 4.0 in Oil & Gas. On the frontline of pipeline operations, control room engineers face daily challenges to keep pipeline infrastructure operating effectively and safely. Ensuring the availability of critical systems is a requisite for Oil & Gas pipeline performance and safety.
- Convergence of OT and IT with limited resources. With finite IT resources, the responsibility for managing critical infrastructure may fall to those on the business operations side. Operations technology (OT) professionals who manage SCADA, DCS, and PLCs may be responsible for deploying new applications and IT architecture themselves. They need the ability to provision IT systems without IT support.
- Security is a significant factor for remote assets. Security and cyber-attack prevention are particular concerns for remote assets as more machinery and equipment seek to enable IIoT sensors for performance analytics. Operators require distributed computing platforms that secure equipment across the supply chain, whether monitoring pipeline sections or performance at pump stations.
Edge Computing
Edge Computing is the perfect cornerstone to a successful digital transformation effort in oil and gas. By maximizing uptime and providing real-time access to mission-critical data, Edge Computing helps upstream and midstream companies maximize their impact on the environment, worker and asset safety, and bottom-line profits.
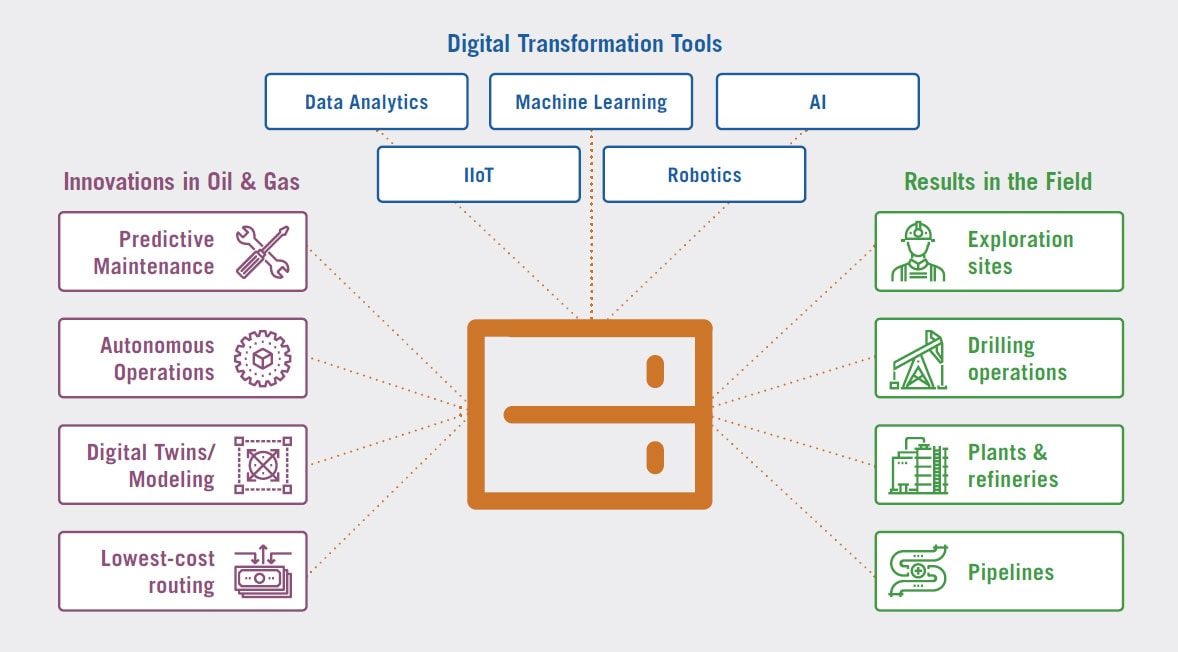
By the nature of their assets and operations, Midstream companies require a new IT architecture to foster digital transformation. They need the ability to run mission critical applications close to their assets. To get there, they need to move computing resources to where they’re needed—at the industrial edge.
Midstream companies now have the opportunity through new Edge Computing platforms to deploy distributed computing architectures that extend mission critical software applications to the edge of their operations for real-time data acquisition, advanced monitoring and control, and asset management— with the net opportunity to accelerate Industry 4.0 in Midstream Oil & Gas. As seen over recent decades, investments in digital technology have delivered operational efficiency, competitive advantage and resilience against industry shocks.
Edge Computing platforms: A foundation for transformation of Midstream operations
Edge Computing enables Midstream operators to restructure their data management strategy using a distributed information architecture to collect and process data at the furthest point a.k.a. “edge” of a computer network. In this distributed model, the secure collection and processing of data takes place locally (at the pump, pipeline or remote data closet, for example) with limited or no connectivity to a centralized cloud or remote data center. Once acquired, data may be sent on-premises to a central control room or to the cloud for analysis and management. This close proximity to equipment reduces latency and balances bandwidth utilization, two factors that constrain the scale and capacity of legacy hardware.
Industrial Edge Computing platforms incorporate a redundant architecture to maximize application availability, provide fault tolerance, and minimize interruptions caused by a single point of failure. They also deliver server performance in a ruggedized form factor that is ideal for Midstream environments and requires zero IT touch. This industrial grade design enables them to be installed at the edge, directly alongside compressors, pumps, or other equipment at terminals and pipelines. Edge Computing platforms purpose-built for the industrial edge also meet IT and security standards out-of-the-box to enable fast implementation that meet IT requirements but do not require IT resources to deploy.
Lastly, modern Edge Computing platforms provide highly efficient operations through virtualization, allowing multiple applications to run on a single node. These solutions reduce IT footprint and maintenance, delivering lower total cost of ownership.
With its flexibility, high availability, fault tolerance, and distributed architecture, Edge Computing provides the foundation for data acquisition and data flow for mission critical operations, and is a pre-requisite for advanced capabilities such as predictive analytics, Digital Twin, and other Industry 4.0 solutions.
Edge Computing deployments that enable operational excellence

Operational excellence is paramount for Midstream—and companies can apply Edge Computing to drive the type of operational excellence achieved in other industries that has resulted in higher customer satisfaction. Three ways operators are deploying Edge Computing platforms to enable operational excellence:
- Visibility on Product Movement and Logistics. The lifeblood of Midstream operations is the ability to accurately track and account for gas and liquids movement for customers and regulatory reporting. Midstream companies are turning to Edge Computing platforms to secure transaction accounting and provide data flow for data management services. Moving Edge Computing to terminal stations delivers visibility and real-time insight into operations that provide decision support and customer satisfaction.
- Asset Performance Management for Equipment Uptime. In recent years, Oil & Gas has seen significant interest and investment in asset performance management solutions to enable predictive maintenance through analysis and condition-based monitoring of critical assets. As with any process operations, Midstream requires equipment availability; unplanned downtime is costly and unacceptable. By acquiring asset performance data at the equipment location, Edge Computing provides real-time visibility into conditions unfolding in the field such as power interruptions, pipeline integrity failures, equipment failure, and other critical issues.
- Advanced monitoring and control to optimize equipment and utilities. Edge Computing is often deployed at compressor and pump stations to provide process monitoring and control with fault-tolerant edge servers deployed in control centers to run SCADA and DCS software. Additionally, Edge Computing is able to run data historians to collect time-based data sets for comparison and analysis against expected parameters. Such application offers Midstream companies the means to optimize utility consumption for energy management.
The ability of Edge Computing platforms to run multiple applications on a single, high availability node through virtualization offers tremendous cost savings and fast deployment of applications. A single piece of hardware may run multiple workloads, for example SCADA and historian software, from large industrial software vendors like AVEVA, Inductive Automation, Rockwell, Schneider Electric, and Siemens in addition to specialized advanced analytics and optimization applications.
Edge Computing unlocks advanced Industry 4.0 capabilities
An effective Edge Computing strategy places advanced analytics applications within grasp for Midstream operators. Notably, they are positioned to finally harvest vast amounts of potential equipment data that lies untapped due to the lack of current computing infrastructure able to capture the additional real-time data.
By further leveraging Edge Computing platforms to gain insight, companies lay a foundation to pursue advanced Industry 4.0 capabilities such as:
- Industrial IoT (IIoT): Technology improvements have reduced cost of IIoT devices, making it now possible to install sensors in machinery and equipment that were previously unavailable. This helps upstream and midstream producers collect, process, and analyze meaningful data in real time to provide more value-producing and cost-saving opportunities. IIoT now provides far greater capabilities to make better use of growing volumes of data, and then act on new insights gained from that data.
- Predictive maintenance: Today, powerful predictive maintenance software can also analyze sensor data—for example from machinery, pipelines, and even tankers—to detect various abnormalities (fatigue, cracks, corrosion, and more) and use this to perform proactive maintenance. For example, midstream companies use predictive maintenance in logistics to help prevent accidents and improve safety in transportation and logistics.
- Digital twins: In Oil & Gas, digital twins are virtual models that combine the virtual and physical worlds. Digital twins improve the analysis of data and system monitoring in a way that improves design and operations, helps prevent downtime, reduces maintenance costs, and provides new data to add value throughout the lifecycle of the oil and gas asset.
- Autonomous operations: Today, autonomous drilling technology is transforming Oil & Gas exploration. Advancements in robotics, sensors, and electronics can now eliminate potentially dangerous manual efforts and perform drilling and other tasks in a safe, reliable, and highly precise way.
- Artificial Intelligence (AI) and Machine Learning (ML): Oil & Gas has long turned to data analytics, especially when it comes to using extremely large amounts of data to make technical and business decisions. Securing the flow of real-time data from the operational edge offers Midstream companies the same level of analytics Owner-Operators enjoy inside the fence. The next phase is employing AI in areas of decision support and asset performance, predicated on the availability of data and information.
What industry leaders require: simple, protected, and autonomous platforms
Edge Computing platforms offer the ability to extend powerful, mission critical applications to the operational edge while simplifying IT management, reducing IT footprint, and offering zero-touch operation. Key attributes operations and technology professionals must look for include:
Simple. For rapid time to value and simple management, potentially by non-technical staff, Edge Computing platforms must be easy to install, deploy, and manage across applications and infrastructure. Systems should also offer virtualization to quickly provision applications, offer flexibility, maximize computing resources, and lower cost of ownership. For pipeline applications, choosing easy-to-commission updates that can be remotely deployed further simplifies management.
Protected. Security is a critical factor for Midstream operations. Edge Computing platforms must secure operational, financial, and reputational risk by ensuring “always on” availability and securing data from cyber threats or data loss. Companies need to select solutions that deliver confidence in security as more devices and systems become connected.
Autonomous. A core promise of Edge Computing is the ability to operate reliably in edge locations such as marine terminals or production plants. Platforms must run in any environment and deliver zero-touch computing that does require human monitoring, maintenance, repairs, or support. Edge Computing platforms that offer “call home” features and 24x7x365 support further minimize any chance of unplanned downtime for equipment and applications.
Gain a competitive advantage with Edge Computing
Midstream operators must evaluate and select from a wide range of digital tools, both to help them overcome traditional challenges and to capitalize on emerging opportunities. A successful digital transformation effort can be a powerful advantage in improving all facets of their business.
Edge Computing is the ideal foundation for Midstream operators to accelerate digital transformation and enable equipment reliability, application availability, and new operational insight by capturing data at the point of origin. In doing so, Midstream companies can achieve the results that matter most: increased employee safety, improved decision making and visibility, operational excellence, lower carbon footprint, and increased customer satisfaction for greater profitability.
About Stratus
For leaders digitally transforming their operations in order to drive predictable, peak performance with minimal risk, Stratus ensures the continuous availability of business-critical applications by delivering zero-touch Edge Computing platforms that are simple to deploy and maintain, protected from interruptions and threats, and autonomous. For 40 years, we have provided reliable and redundant zero-touch computing, enabling global Fortune 500 companies and small-to-medium sized businesses to securely and remotely turn data into actionable intelligence at the Edge, cloud and data center— driving uptime and efficiency. For more information, please visit stratus.com.